Due to low surface energy, low shear strength and low elastic modulus, polymers usually have low friction when they are used for tribological applications. However, the wear resistance of the polymers can be an issue for many applications, especially for extreme working conditions such as high load, high speed and high temperature conditions.
Aromatic Thermosetting Polyester (ATSP) based tribology coatings, which are sold under ATSP’s NOWE™ tradename, have extreme high wear resistance under these harsh conditions.
In this case study, the tribological performance of NOWE™ coating is compared with that of PTFE and PEEK based coatings under pin-on-disk experimental configuration, as shown in the figure below. The working conditions of tilting pad bearing with starved lubrication condition were simulated for this particular study.
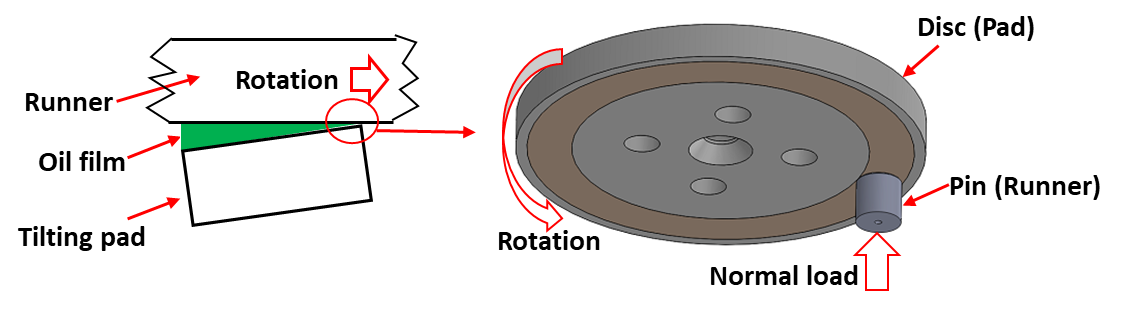
Tribological testing setup for coatings
The electrical submersible pumps (ESPs) are used to pump crude oil out of the oil wells in the oil and gas industry. The lubricant film of the thrust bearing in ESPs can be broken by the high load and high temperature, and potentially leading to seizure and scuffing of the bearing interface.
For the tribological testing, the metal pin was designed to slide on the coatings (NOWE™, PEEK (1704 PEEK/PTFE®) and PTFE (DuPont 958G-414®) with 10s of micron thickness. The coatings are deposited on the C93200 bronze disk. The sliding conditions were: speed of 2.4m/s, contact pressure of 13 MPa and sliding distance varied from 25.9 to 155.5 Km. One drop of lubricant is added on top of the pin for every 25.9 Km sliding, generating the starved lubrication condition. The near contact temperature in this sliding can be as high as 150 °C.
Among the three coatings investigated, NOWE™ coating showed the lowest wear rate, as low as 4.15x10-8 mm3/Nm after a sliding distance of 155.5 Km (corresponding to more than 1.08 million cycles). In the figure shows the optical micro images of wear scar of the three coatings after 25.9 Km sliding distance: NOWE™ coating has the highest wear resistance (only burnishing of the peaks of the coating), followed by PTFE based coating, and PEEK coating, both had clear abrasive wear scars.
As shown in the table, assume the same wear rate during the sliding, with a 40 μm thickness coating, NOWE™ coating can run over 2216 Km sliding distance, corresponding with over 15 million cycles, which is 13.4 and 24.8 times of running life of PTFE based and PEEK based coating, respectively.
Coatings
|
PEEK coating
|
PTFE coating
|
NOWE coating
|
Wear rate (mm³/N*m)
|
1.02 x 10ˉ⁶
|
0.55 x 10ˉ⁶
|
0.0415 x 10ˉ⁶
|
Number of cycles
|
620 K
|
1, 150 K
|
15, 437 K
|
Sliding distance (Km)
|
89 Km
|
165 Km
|
2216 Km
|

Micrographs of coating surfaces after wear
The pin-on-disk experiments of the coatings showed ATSP coating had excellent tribological performance and could be used on the pads of thrust tilting pad bearings, as well as in any high load, high speed and extreme temperature conditions, from -196 to 300 °C.
We can also further customize the NOWE™ coatings to any of your specific needs. Reach out to us at contact@atspinnovations.com or through the website contact form and we will be happy to solve your tribology issues.